Definition of picking in a "manual", semi-automated and 100% automated warehouse
Picking is the action of the "picker" who fetches ordered items, and assembles them for packing and dispatch. In a manual warehouse, these trips can add up to several kilometers a day... Picking is governed by two main principles: the "man-to-item" process, in which the order picker travels to fetch the products; and the "item-to-man" process, in which the item comes to the operator, thus limiting his travels, which can only take place in automated or semi-automated warehouses. This is a dynamic picking configuration, which changes according to logistical challenges, such as product seasonality, or the volume of items to be picked.
In the "man-to-item" process, several methods can be applied: the Pick and Pack method, which requires the picker following a printed list to pick items for one or more orders, and bring them to the packing area. The Put to Light method involves equipping operators with a display caddy, which indicates the location of the items, and where they are to be deposited. Finally, the Pick by Light method also uses lights and messages, which are displayed at the storage location where the items to be picked are located. This makes it easy to see where each item is to be picked. Each of these methods obviously requires a different type of equipment, with varying degrees of cost.
In semi-automated warehouses, for the "item-to-man" process, new technologies are continuously improving the operation of logistics warehouses. Picking can be carried out in two different ways: either robots bring the items to the packing area, or a central conveyor brings them there, as in industrial chains. Computerized processes, such as voice-activated order-picking systems, guide operators, and automated mechanisms help pack orders. However, this requires a number of parameters to be taken into account: starting with shelving, dynamic racks and shelving units, which need to be adapted to the chosen picking method; a precise labeling system to assist the operator with optimal product traceability; electronic terminals to locate the picking location and the place where orders can be deposited for packing; and finally, handling aid equipment, such as connected trucks, forklifts or pallet trucks.
Other large warehouses are 100% automated and computerized. In these cases, data alone determines the operators' picking path.
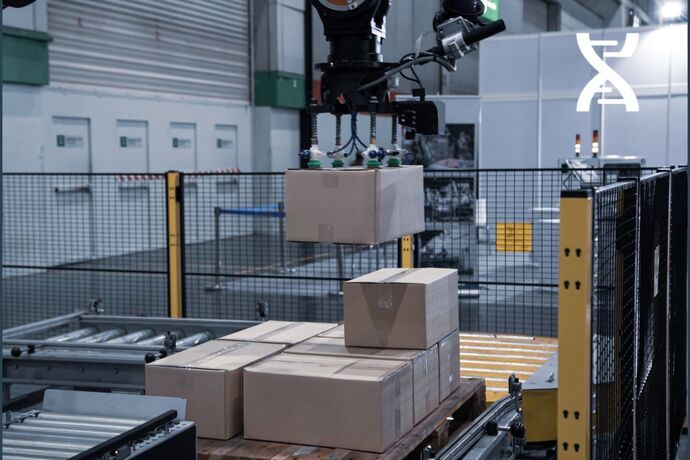